Kapton tape, a polyimide film tape, has gained significant attention in various industries due to its unique properties and versatility. This specialized tape is known for its high-temperature resistance, electrical insulation capabilities, and chemical stability, making it an essential tool in many applications. In this article, we will explore what Kapton tape is used for and how it differs from regular tape.
What is Kapton Tape Used For?
Kapton tape is primarily used in environments that require high thermal resistance and electrical insulation. Here are some of its most common applications:
Electronics Manufacturing: One of the most prevalent uses of Kapton tape is in the electronics industry. It is often used to mask off areas during soldering and painting processes. Its ability to withstand high temperatures without melting or degrading makes it ideal for protecting sensitive components from heat damage.
3D Printing: In the realm of 3D printing, Kapton tape is frequently used as a build surface for printers. The tape provides excellent adhesion for various filament types, including ABS and PLA, ensuring that the printed object sticks to the surface during the printing process. Additionally, it can withstand the high temperatures generated by the heated print bed.
Aerospace Applications: Kapton tape is widely used in the aerospace industry due to its lightweight and high-performance characteristics. It is employed in the insulation of wires and cables, as well as in the assembly of spacecraft components. Its ability to endure extreme temperatures and harsh environments makes it a reliable choice for aerospace engineers.
Automotive Industry: In automotive applications, Kapton tape is used for insulation and protection of electrical components. It helps prevent short circuits and protects sensitive parts from heat and chemicals, ensuring the longevity and reliability of automotive systems.
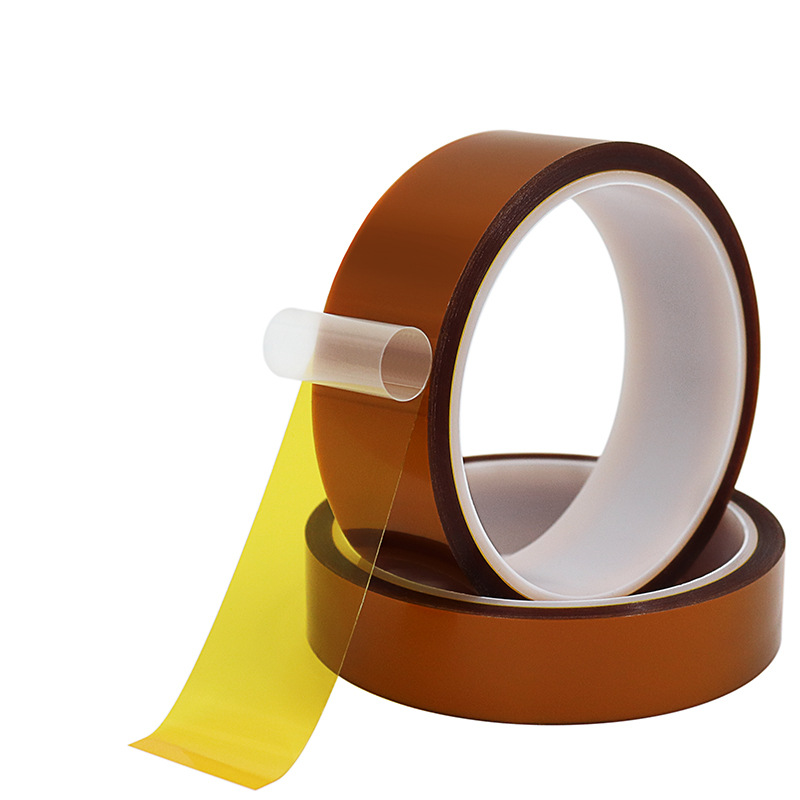
What is the Difference Between Kapton Tape and Regular Tape?
While Kapton tape shares some similarities with regular tape, several key differences set it apart:
Material Composition: Kapton tape is made from polyimide film, which provides its unique properties. In contrast, regular tape is often made from materials like paper, plastic, or cloth, which do not offer the same level of heat resistance or electrical insulation.
Temperature Resistance: One of the most significant differences is the temperature tolerance. Kapton tape can withstand temperatures ranging from -269°C to +400°C (-452°F to +752°F), making it suitable for high-temperature applications. Regular tape, on the other hand, typically has a much lower temperature threshold and may melt or lose adhesion when exposed to heat.
Electrical Insulation: Kapton tape is an excellent electrical insulator, making it ideal for use in electronic applications. Regular tape may not provide the same level of insulation and could potentially conduct electricity, leading to short circuits or other electrical issues.
Chemical Resistance: Kapton tape is resistant to a wide range of chemicals, including solvents and oils. This property makes it suitable for use in environments where exposure to harsh substances is a concern. Regular tape may not have the same level of chemical resistance and could degrade when exposed to certain chemicals.
Adhesive Properties: The adhesive used in Kapton tape is designed to maintain its bond under extreme conditions, including high temperatures and exposure to various chemicals. Regular tape may not have the same durability and could lose its adhesive properties over time or when subjected to heat.
Cost: Due to its specialized properties and manufacturing process, Kapton tape is generally more expensive than regular tape. However, its durability and performance in demanding applications often justify the higher cost for professionals and industries that rely on its unique characteristics.
Post time: Feb-27-2025